Truth About Cast Steel Henry Bessemer a spectacular liar
“Henry Bessemer was so bitter about Cast Steel being better than his [Forged] Steel that he told spectacular lies about it.” – 0:37 in
The Strength Behind Cast Steel: A Comprehensive Guide
Cast steel is a versatile and essential material in industries ranging from construction and automotive to mining and heavy machinery. Known for its strength, durability, and adaptability, cast steel has played a pivotal role in shaping modern engineering and manufacturing. But what exactly is cast steel, and what makes it such a valuable resource?
What is Cast Steel?
Cast steel is a type of steel that is melted and poured into molds to create specific shapes and structures. It typically consists of iron, carbon, and other alloying elements like manganese, chromium, or nickel. The casting process allows for the production of complex shapes and detailed designs that would be difficult or impossible to achieve through other manufacturing methods.
Key Properties of Cast Steel
- Strength and Durability
Cast steel is known for its exceptional mechanical strength, making it suitable for applications requiring heavy loads and high impact resistance. - Versatility
The ability to customize alloy compositions gives cast steel its versatility. It can be tailored for specific applications, from wear-resistant tools to high-tensile-strength components. - Corrosion and Heat Resistance
Depending on the alloy composition, cast steel can offer superior resistance to corrosion, oxidation, and high temperatures, making it ideal for harsh environments. - Machinability
Despite its strength, cast steel is relatively easy to machine and weld, which adds to its appeal in industrial applications.
Applications of Cast Steel
Construction and Infrastructure
Cast steel components are often used in bridges, buildings, and heavy-duty frameworks. Their ability to withstand immense stress and strain makes them indispensable in these applications.
Automotive and Transportation
From engine components to structural parts, cast steel plays a crucial role in the automotive industry. Its durability ensures safety and reliability in vehicles.
Mining and Heavy Machinery
Mining equipment and heavy machinery rely on cast steel for parts like gears, brackets, and housings. The material’s toughness ensures long service life under extreme conditions.
Energy Sector
In the energy industry, cast steel is used for turbines, valves, and pressure vessels, where strength and heat resistance are critical.
Benefits of Cast Steel Over Other Materials
- Design Flexibility: The casting process allows for intricate shapes and unique designs.
- Cost Efficiency: Large-scale production can be more cost-effective compared to forging or machining.
- Wide Range of Alloys: Customizing properties like hardness, ductility, and tensile strength is possible through alloying.
Challenges and Innovations in Cast Steel Production
While cast steel is highly advantageous, its production process can be energy-intensive and requires precision to avoid defects. Innovations like vacuum casting, 3D-printed molds, and advanced alloy development are addressing these challenges and pushing the boundaries of what cast steel can achieve.
Conclusion
Cast steel remains a cornerstone of modern manufacturing and engineering, offering unmatched strength, versatility, and adaptability. As technology evolves, so too will the applications and innovations surrounding this incredible material.
Whether you’re constructing a skyscraper, building a vehicle, or manufacturing machinery, cast steel is the unsung hero ensuring durability and reliability at every turn.
The Bessemer Process: Revolutionizing Steel Production
The Bessemer Process marked a pivotal moment in industrial history, transforming steel production and fueling the growth of modern infrastructure. Named after its inventor, Sir Henry Bessemer, this revolutionary method for mass-producing steel dramatically reduced costs and increased efficiency, shaping industries worldwide.
What is the Bessemer Process?
The Bessemer Process, developed in the 1850s, is a steel-making method that involves blowing air through molten pig iron to remove impurities such as carbon, silicon, and manganese. The process takes place in a specially designed container called a Bessemer Converter, which allows for rapid oxidation and purification of the iron.
How It Works
- Molten Pig Iron Introduction
Pig iron, the raw material, is poured into the Bessemer Converter. - Air Injection
High-pressure air is blown through the molten iron. This creates a chemical reaction where impurities oxidize and either burn off as gases or form a slag that can be removed. - Steel Refinement
Once the desired carbon content is achieved, alloying elements like manganese or silicon may be added to refine the steel further. - Pouring the Steel
The purified molten steel is poured into molds for cooling and shaping.
Advantages of the Bessemer Process
- Cost-Effective Production
By significantly reducing labor and fuel costs, the Bessemer Process made steel production cheaper and accessible on a large scale. - Rapid Manufacturing
The process could produce steel in minutes, compared to the hours required by older methods. - Higher Quality Steel
The removal of impurities resulted in stronger, more durable steel, ideal for industrial use. - Scalability
It allowed for mass production, meeting the growing demand for steel in construction, transportation, and manufacturing.
Impact on Industry and Society
Railroads and Transportation
The availability of inexpensive steel fueled the expansion of railroads, connecting cities and fostering economic growth.
Construction Boom
Stronger and more affordable steel made iconic structures like bridges and skyscrapers possible, ushering in the age of modern architecture.
Industrial Revolution
The process played a key role in powering the Industrial Revolution, enabling the development of machinery, tools, and infrastructure.
Challenges and Limitations
While the Bessemer Process was groundbreaking, it wasn’t without its flaws:
- Quality Control Issues: Early methods struggled to produce consistent results.
- Sulfur and Phosphorus Impurities: The process couldn’t remove these elements, making it less effective for certain ores.
- Environmental Concerns: The large-scale burning of impurities created pollution, a concern that persists in modern steel-making.
Legacy and Modern Replacements
The Bessemer Process eventually gave way to more advanced methods, like the Open-Hearth Process and the Basic Oxygen Process (BOP), which offered greater control and flexibility. However, its historical significance remains undisputed.
Conclusion
The Bessemer Process stands as a testament to human ingenuity and innovation. By revolutionizing steel production, it not only laid the foundation for modern industry but also shaped the physical and economic landscape of the world. Its legacy lives on in the towering skyscrapers, expansive bridges, and networks of railroads that define our civilization.
Comparing and Contrasting Steel and Iron Production Techniques
Steel and iron have been foundational to human civilization, with various production methods emerging over centuries. Here’s a comparison of Damascus Steel, Crucible Steel Process, Bessemer Process Steel, Forged Steel, Cast Iron, and Pig Iron, focusing on their properties, production methods, and uses.
1. Damascus Steel
- Production Method:
Originating in the Middle East, Damascus Steel was crafted by forging together layers of high-carbon and low-carbon steel, producing a characteristic wavy pattern. The process involved repeated folding and hammering. - Properties:
- Strong and flexible.
- Resistant to shattering.
- Decorative wavy patterns due to layered construction.
- Uses:
Primarily used in swords, knives, and other bladed weapons. - Strengths:
Aesthetic beauty combined with functional toughness. - Limitations:
The original technique was lost, and modern replicas rely on pattern welding.
2. Crucible Steel Process
- Production Method:
Developed in South Asia and later refined in Europe, crucible steel was made by melting iron and carbon in a sealed clay crucible, achieving higher temperatures and uniform carbon distribution. - Properties:
- High purity.
- Uniform microstructure.
- Enhanced hardness and durability.
- Uses:
Tools, weapons, and industrial machinery. - Strengths:
High-quality steel with consistent properties. - Limitations:
Labor-intensive and time-consuming, making it expensive.
3. Bessemer Process Steel
- Production Method:
Invented in the 1850s, this method used a Bessemer Converter to blow air through molten pig iron, removing impurities like carbon, silicon, and manganese. - Properties:
- Mass-producible.
- Moderate quality steel, suitable for construction and industrial use.
- Uses:
Railroads, bridges, buildings, and general infrastructure. - Strengths:
Cost-effective, scalable, and fast production. - Limitations:
Impurities like sulfur and phosphorus couldn’t be effectively removed.
4. Forged Steel
- Production Method:
Involves heating steel and shaping it using compressive forces like hammering, pressing, or rolling. - Properties:
- Extremely strong and durable.
- Resistant to impact and fatigue.
- Uses:
Automotive components, aerospace parts, and tools. - Strengths:
Excellent mechanical properties and structural integrity. - Limitations:
Limited to simpler shapes compared to casting.
5. Cast Iron
- Production Method:
Made by melting iron and pouring it into molds. Contains 2-4% carbon, along with silicon and other elements. - Properties:
- Brittle but strong in compression.
- Resistant to wear and deformation.
- Uses:
Engine blocks, pipes, cookware, and construction elements. - Strengths:
High wear resistance and cost-effective for complex shapes. - Limitations:
Brittle, with low tensile strength, making it unsuitable for applications involving high impact.
6. Pig Iron
- Production Method:
The raw output of a blast furnace, pig iron is an intermediate product with high carbon content (4-5%) and impurities like sulfur and phosphorus. - Properties:
- Brittle and unrefined.
- High carbon content makes it hard but weak.
- Uses:
Used as a precursor for producing steel or cast iron. - Strengths:
Essential for further processing into steel or cast iron. - Limitations:
Not useful in its raw form due to brittleness.
Comparison Table
Material/Process | Carbon Content | Strength | Brittleness | Production Ease | Typical Use Cases |
---|---|---|---|---|---|
Damascus Steel | ~1.5-2% | High (flexible) | Low | Labor-intensive | Swords, knives, decorative items |
Crucible Steel | 1-2% | High (uniform) | Low | Labor-intensive | Tools, weapons, machinery |
Bessemer Steel | ~0.2-1% | Moderate | Low | Highly scalable | Railroads, buildings, bridges |
Forged Steel | ~0.2-1% | Very High | Very Low | Moderate | Aerospace, automotive, tools |
Cast Iron | 2-4% | High (compression) | High | Easy | Pipes, engine blocks, cookware |
Pig Iron | 4-5% | Low | Very High | Easy | Raw material for steel/cast iron |
Key Takeaways
- Damascus Steel and Crucible Steel prioritize craftsmanship and high quality but are labor-intensive and costly.
- Bessemer Process Steel revolutionized industry with its scalability and cost-efficiency but had limitations in impurity removal.
- Forged Steel offers unparalleled strength for demanding applications, while Cast Iron is versatile for non-structural uses.
- Pig Iron is crucial as a starting material for further refinement into more usable forms.
Each material or process serves specific purposes, reflecting the balance between performance, cost, and application needs.
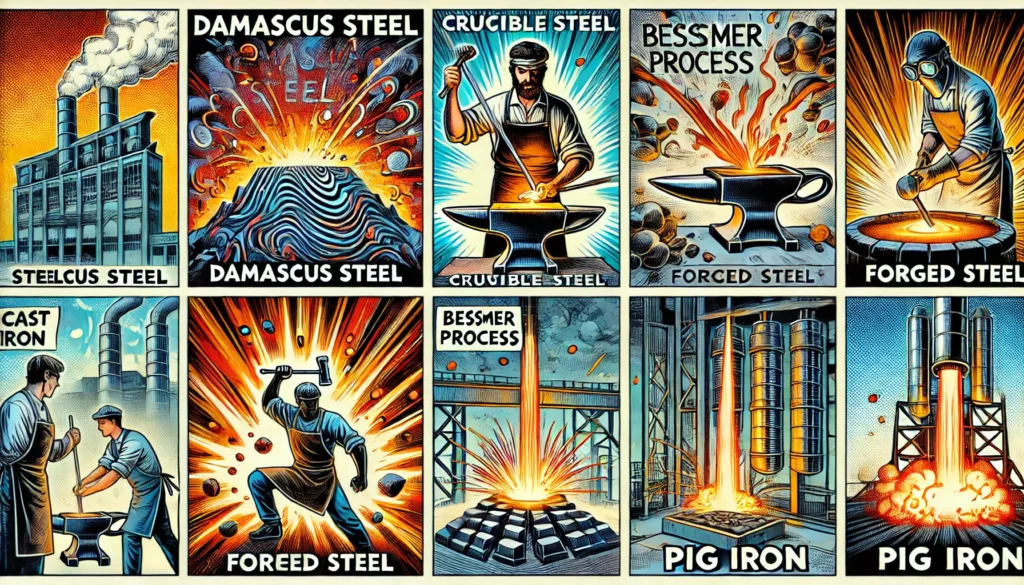